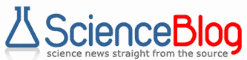
September 2002 From Technical Insights Product development finds new ally in rapid freeze prototyping Technical Insights' Advanced Manufacturing Technology AlertSAN ANTONIO--September 9, 2002--Rapid prototyping (RP) technology has just found a new ally - water. A new technique called rapid freeze prototyping (RFP) is attempting to improve upon the rapid prototyping process by deploying ice rather than traditionally used plastics to construct models. Rapid prototyping has enabled product manufacturers to develop their products at a more rapid rate and at lower costs for the intensely competitive global market. Currently, however, most rapid prototyping systems are extremely expensive. Many of them also pose considerable health hazards since they generate dust and smoke. In contrast, rapid freeze prototyping is likely to provide immense benefits in terms of costs, time, and health. Rapid freeze prototyping is expected to not only condense the time required to produce a prototype from days to mere hours, but is also regarded as being potentially cleaner than the conventional rapid prototyping systems. Moreover, because water is less expensive than plastic polymers, the process is expected to be more economical than traditional rapid prototyping. Manufacturers are likely to profit from the lower working costs and heightened speed of rapid freeze prototyping systems. The ease of building both transparent and color parts, the latter through the simple method of adding food coloring to the water stream, is expected to offer an additional advantage. Rapid freeze prototyping works in a mode comparable to other rapid prototyping techniques. Droplets of water are deposited from a nozzle onto a surface, similar to the procedure utilized for plastics in other systems. However, the techniques diverge at this point. The rapid freeze prototyping process occurs within a freezing chamber, which enables the fabricated part to remain whole. Rapid freeze prototyping technology is still at the developmental stage. Compared with other prototyping methods, it is less expensive, faster, and much cleaner. But it is also very challenging because it requires a controlled environment for the process. However, this scenario is set to change. Two sizeable grants from the National Science Foundation (NSF) are likely to stimulate research initiatives in future. One grant has been allocated toward a one-year feasibility study of an investment casting method for rapid freeze prototyping. The other will be used to scrutinize the viability of using the method for generating molds for dental restorations, such as bridges, implants, and crowns. New analysis by Technical Insights, a business unit of Frost & Sullivan (www.ti.frost.com) featured in Advanced Manufacturing Technology Alert, highlights the research projects that are likely to underline the value of rapid freeze prototyping as a preferred alternative to other prototyping methods. Frost & Sullivan is a global leader in strategic market consulting and training. Acquired by Frost & Sullivan, Technical Insights is an international technology analysis business that produces a variety of technical subscriptions and growth consulting services. Ongoing analysis on rapid freeze prototyping is available in Advanced Manufacturing Technology Alert, a Technical Insights subscription service. Interviews are available to the press. Contact: Julia Rowell P: 210.247.3870 F: 210.348.1003 E: jrowell@frost.com www.frost.com www.technical-insights.frost.com |